Critical Properties for Etch Chamber Plastics
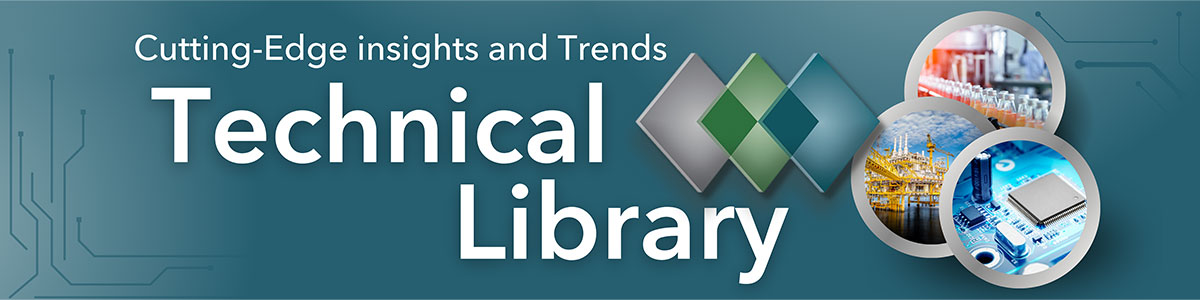
When designing process tools for IC chip manufacturing, engineers must carefully select plastic materials that can survive extreme chamber conditions. One of the most aggressive environments in semiconductor fabrication is the dielectric etch chamber, where plastics are exposed to the combined assault of gas plasma, high temperatures, vacuum pressure, and RF energy.
No plastic survives indefinitely in these conditions—the goal is to identify materials that perform as long as possible while minimizing ionic contamination risk.
Why Plastics Are Still Used in Etch Chambers
Despite increasing electrode power in modern etch tools, plastics remain relevant because of their insulating properties and design flexibility—something quartz and ceramics can’t always offer. However, traditional datasheet specs aren't enough. You need deeper performance data to make the right call.
Key Properties to Evaluate
1. Oxygen Plasma Resistance
Chambers that use oxygen plasma for cycle flushing expose materials to one of the harshest environments possible. Energized oxygen aggressively attacks polymer chains, particularly the double carbon bonds (C=C) in the material structure. A plastic’s chemical makeup, combined with its thermal tolerance, dictates its survivability.
2. Etching Gas Plasma Resistance
Etch gases—typically fluorine or argon-based—are used to sculpt microscopic circuit paths. From a polymer standpoint, think of these gases as a nano-scale sandblaster. Hardness and thermal stability often correlate with how long a material lasts in these chambers. Stronger surfaces tend to survive longer under bombardment.
3. Ionic Purity
Plastics exposed to plasma eventually erode, and their residual metal content can become a contamination threat to wafers. A clean breakdown (i.e., low ion residue) is ideal. However, if a material has high metal content but resists erosion, the risk is minimized. What matters most is knowing both the rate of erosion and ionic purity—especially in proximity to the electrode.
Direct vs. Indirect Plasma Exposure
Location matters. A plastic directly facing the electrode will degrade much faster than one indirectly exposed. Understanding application geometry is critical to extending RF life and reducing contamination risk.
Selecting plastics for etch chambers isn’t just material science—it’s process-critical strategy.
To ensure optimal performance in etch environments, you need the right testing data and application-specific recommendations.
Need help selecting plastics for dielectric etch chambers? Contact your local Port Plastics sales office or visit www.PortPlastics.com.
Download As PDF |