Beverage
Industrial Beverage equipment is one of the fastest-growing segments. The world is estimated to produce a staggering 1.1M bottles of water every minute, approaching nearly 600B annually. Beverage Equipment requires ultra-precision timing and wear components to have an exceptional life expectancy. Subtle deviations in performance can lead to substantial losses to efficiency and profitability. Port Plastics' portfolio of extreme wear materials provides equipment designers with cutting edge next generation material solutions
Beverage Component Applications
Beverage equipment operates at extreme speeds for extended periods in a wide range of environmental conditions. Moving components operate in varying pressures and velocity (PV), inducing frictional heat. Materials are commonly selected based on their ability to resist wear (K Factor), resistance to loading at temperature (HDT), and resistance to frictional heat (PV). Selecting the proper material(s) for precision machined parts is critical to the performance of processes such as mixing, sealing, and capping. Beverage systems operate between 32F - 250F and materials are chosen based on:
- Chemical or pH resistance
- Abrasion resistant
- Non-Sticking
- Resistant to Chipping
- Sliding Properties
- Detection
Typical applications:
- Valves
- Grippers
- Profile Guides
- Cappers / Sealers
- Timing Screw
- Transfer Sprockets.
Common materials used in wafer component applications:
- HDPE
- UHMW
- PA6
- PET
- POM
- PTFE
- Tubing
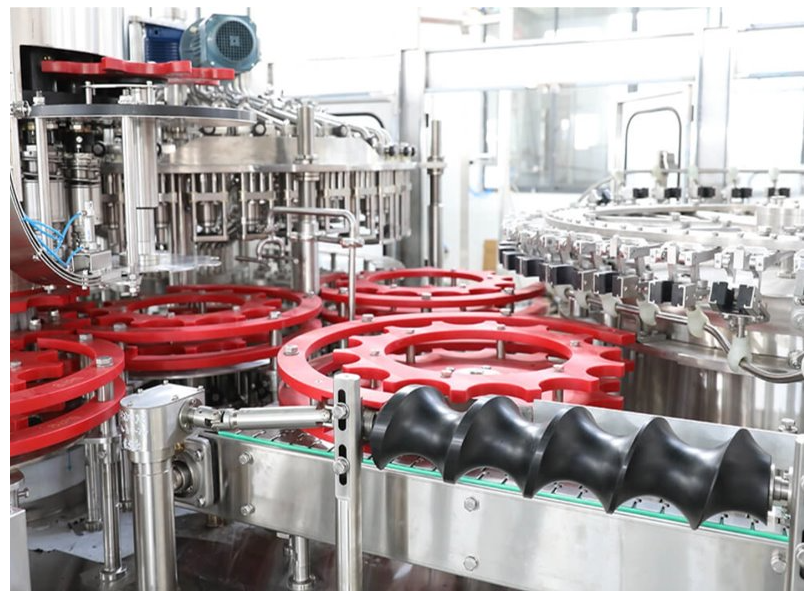
If you design and manufacture automation equipment for the Food, Beverage, and Conveyance industry then you understand the importance of selecting the optimum material for wear performance. In general, wear is mechanically induced surface damage resulting in material progressive removal due to relative motion between two contacting surfaces. On typical property data sheets, “WEAR” is expressed by K-Factor value K = W/(F x V x T). The lower the K factor typically the better the wear resistance.
Wear Factor (K) used to define wear resistance
Lower Value = Better Wear Resistance
K = W/(F x V x T)
WHY IS K-FACTOR PROPERTY OFTEN MISUNDERSTOOD?
ASTM / ISO Standards – Engineers are taught to use quantifiable standards and match them to the specific application needs. In the case of K-FACTOR property, there is no governing ASTM or ISO Test standard. Having no industry standards means that Engineers will need to interpret the manufacturer’s methodology and data.
K = W/(F x V x T) is a variable formula that all manufacturers use to define a material’s specific” WEAR” characteristics. Force, Velocity, and Time are not defined and thus are variables. Each manufacturer uses its own standards for each of these variables.
- Therefore, when comparing Manufacturer A to Manufacturer B, we can not assume it is an apples-to-apples comparison.
-
- We can assume K Factor is a relative constant across a manufacturer's entire product line.
-
- The Test is performed in a dry environment at ambient temperature and does not account for material softening or soluble lubricants, which can greatly impact performance.
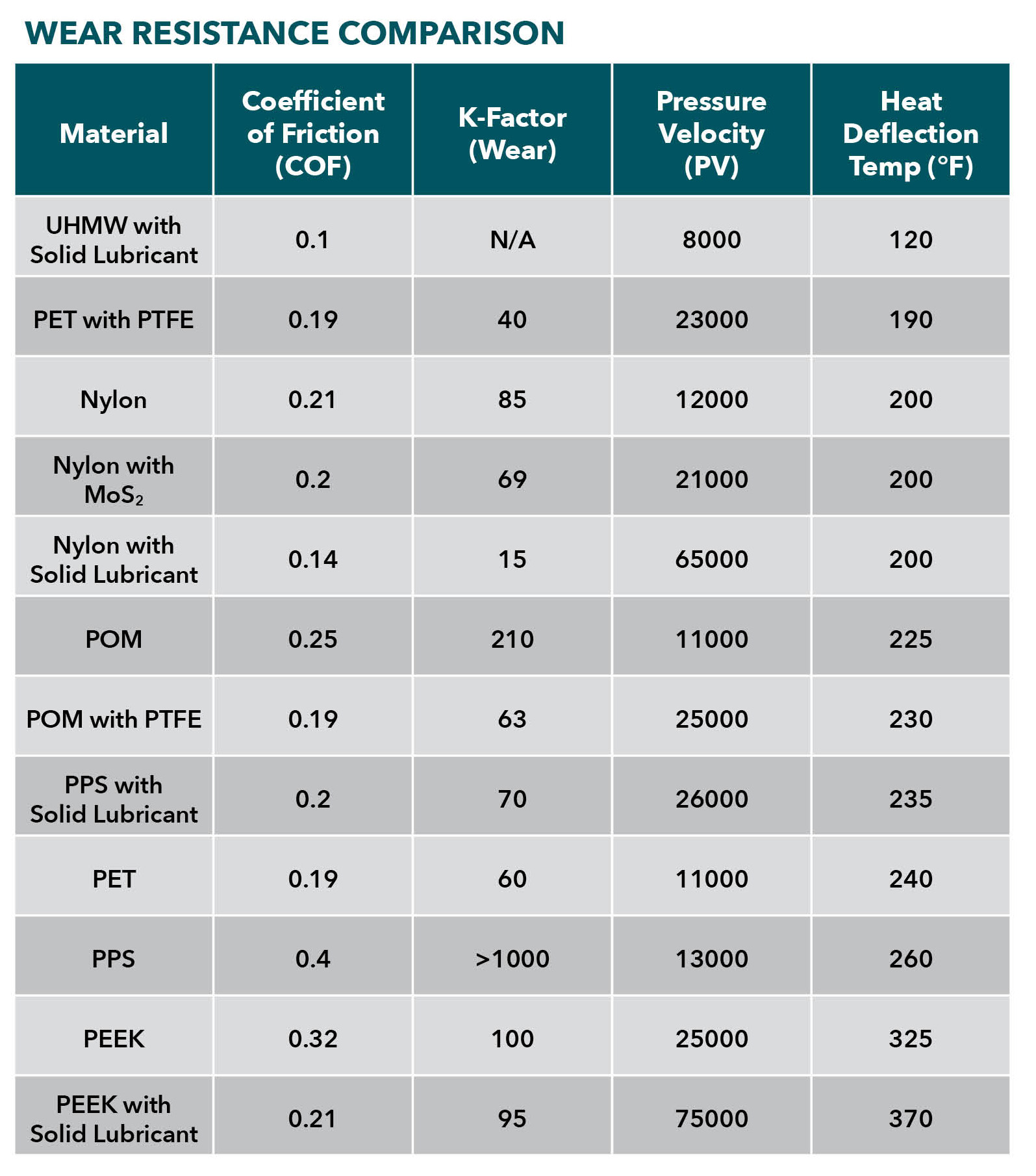